Ensuring Quality Through Precision Measurement & Verification
At Huron, we understand the critical importance of precision in the manufacturing of cutting tools. That's why we employ state-of-the-art measurement techniques and rigorous material verification processes to ensure the highest level of quality.
.jpg)
.jpg)
.jpg)
In-Depth Testing Protocols Ensure Unmatched Quality
We take quality assurance seriously. Our in-depth testing protocols and skilled craftsmanship ensure that our cutting and grinding tools meet the highest standards of performance and reliability.
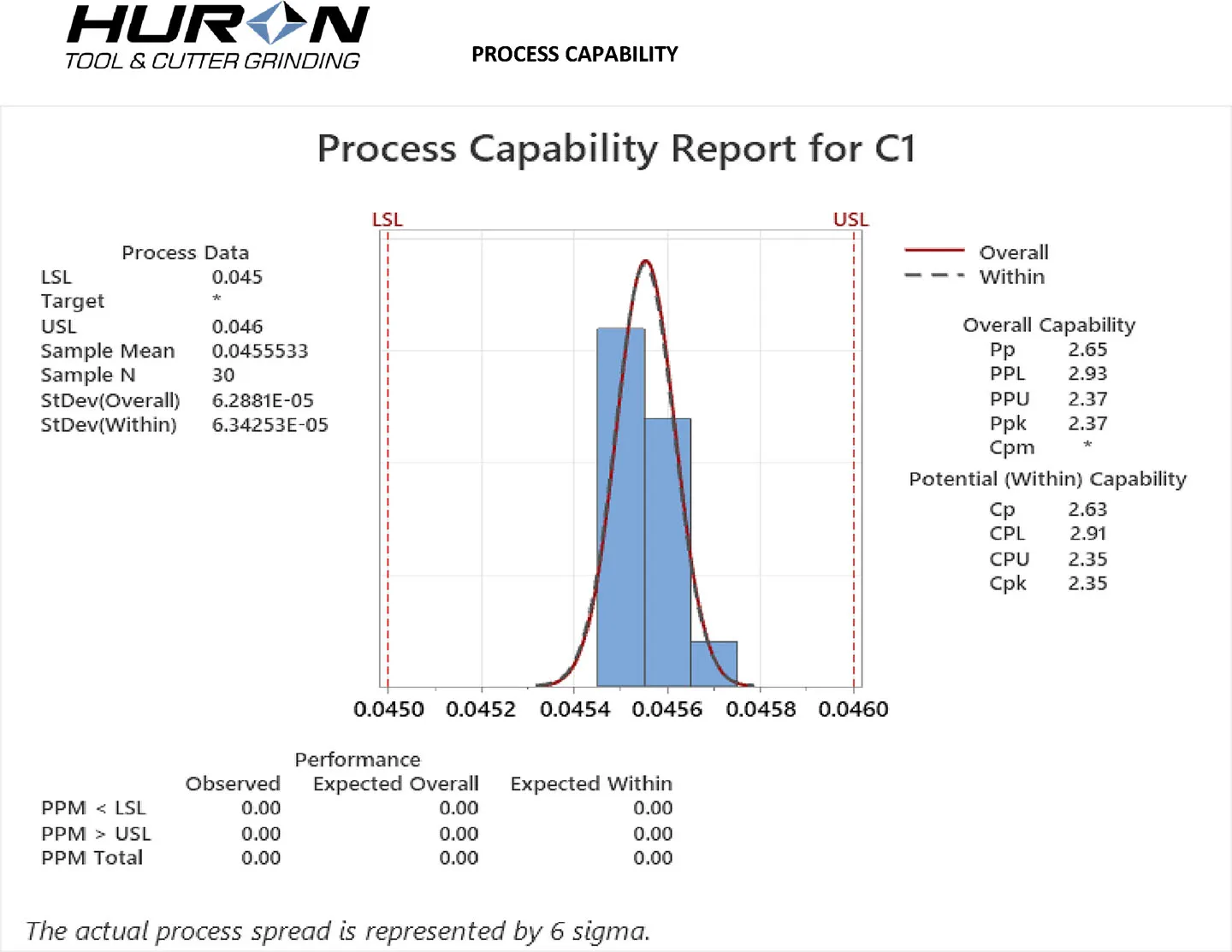
PRODUCTION
PART
APPROVAL
PROCESS
PPAP & DFM
Production Part Approval Process (PPAP) and Design for Manufacturability (DFM) are two critical components in the manufacturing process, each playing a distinct but complementary role in ensuring product quality and efficiency.
To simplify the manufacturing process, reduce production costs, and assure product quality, Huron collaborates closely with our clients during the DFM phase.
Huron’s PPAP process is utilized to ensure that manufacturing processes can produce parts consistently and meet customer requirements. The PPAP process involves validating that all design and production requirements are met and that the production process is capable of reliably producing high-quality parts.
At Huron Tool, we consistently achieve a near 100% quality rating, reflecting our unwavering commitment to excellence and precision in manufacturing.
FAQs
Find answers to common questions about quality standards, certifications, and processes at Huron Tool & Cutter Grinding.
At Huron Tool & Cutter Grinding, we proudly hold ISO 13485:2016 and ISO 9001:2015 certifications. These certifications highlight our expertise in producing medical devices with a focus on safety and efficacy, in addition to our dedication to continuous improvement and customer satisfaction across all aspects of our manufacturing processes.
We employ state-of-the-art measuring equipment and advanced quality control processes to ensure the precision and accuracy of our products. Our skilled technicians perform rigorous inspections and tests at various stages of the manufacturing process to guarantee that every product meets our exacting standards.
Yes, continuous improvement is a core principle at Huron. We regularly review our processes, gather employee suggestions, and analyze customer feedback to identify opportunities for improvement. We implement changes and monitor their effectiveness to ensure ongoing enhancement of our products and services.
Huron has extensive experience in manufacturing high-quality surgical instruments and implants. We have a deep understanding of the unique requirements and regulations in the medical device industry, and we have a proven track record of delivering products that meet the most stringent standards for quality, safety, and performance.
Huron employs a range of robotic systems to support our manufacturing operations. This includes collaborative robots (cobots) that work safely alongside our human operators, as well as fully automated systems for tasks such as CNC machining, laser marking, and material handling. We carefully select and integrate these systems to optimize our workflows and ensure seamless compatibility with our existing equipment and processes.
We are location in Long Island, New York at:485 Smith Street, Farmingdale
Our validated cleaning processes are rigorously tested through IQ, OQ, and PQ protocols, ensuring the highest standards of cleanliness and compliance.
Yes, Huron has a dedicated quality assurance department staffed by experienced professionals. They are responsible for overseeing our quality management system, conducting audits, and ensuring compliance with industry standards and customer requirements.
Yes, Huron offers validation and verification services to support our customers' quality and regulatory requirements. This includes process validation, equipment validation, and software validation, as well as measuring and testing services to verify product dimensions, material properties, and functional performance.
Still have questions?
Don't hesitate to reach out to us – we are here to help you achieve your goals and exceed your expectations. Contact us today to learn more about how Huron Tool & Cutter Grinding can deliver the quality and reliability you demand.